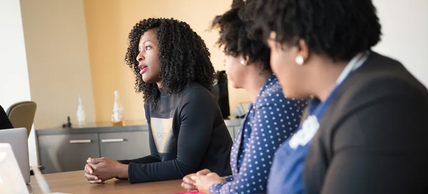
Automotive Engineering Technicians
Median Wage (USD, 2023) | Projected Job Openings (2022-2032) | Projected Growth (2022-2032) | |
---|---|---|---|
National Statistics | $64,020 | 3,500 | 1.90% |
State Statistics | - | - | - |
City Statistics | - | - | - |
Assist engineers in determining the practicality of proposed product design changes and plan and carry out tests on experimental test devices or equipment for performance, durability, or efficiency.